Table of Contents
- Reading Time | 10mins
Introduction
Efficient storage is a critical aspect of logistics and warehouse management. Among the various storage solutions available, pallet racking systems stand out as versatile, space-efficient, and customisable options.
This Ultimate Guide to Pallet Racking Systems aims to provide you with a comprehensive understanding of these industrial racking systems, covering types, configurations, installation tips, and maintenance best practices.
Chapter 1: Understanding Pallet Racking Systems
Definition and Purpose
Pallet racking systems are a form of storage that allows for the systematic arrangement of palletised goods within a warehouse or distribution centre. The primary purpose is to optimise space utilisation while providing easy access to stored items. By utilising vertical space effectively, pallet racking systems contribute to streamlined inventory management and improved workflow efficiency.
Key Benefits
- Space Optimisation: Racking systems make the most of available vertical space, maximising storage capacity without expanding the physical footprint of the warehouse.
Accessibility: With the ability to organise and retrieve pallets easily, these systems facilitate quick and efficient access to stored goods, reducing picking and retrieval times.
Versatility: Pallet racking systems are adaptable to various warehouse environments and cater to different types of goods, making them suitable for a wide range of industries.
Cost-Effective: In comparison to traditional storage methods, pallet racking systems offer a cost-effective solution by optimising space and reducing the need for additional warehouse space.
Throughout this guide, we will delve deeper into the different types of pallet racking systems, their configurations, installation procedures, and the best practices for ongoing maintenance. Let’s explore the diverse world of pallet racking and discover how it can revolutionise your warehouse management.
Chapter 2: Types of Pallet Racking Systems
Efficient storage solutions are crucial for businesses to optimise warehouse space and streamline logistics. Pallet racking systems play a pivotal role in achieving this goal, offering a variety of options tailored to different needs. In this chapter, we will explore the key types of pallet racking systems and their respective advantages.
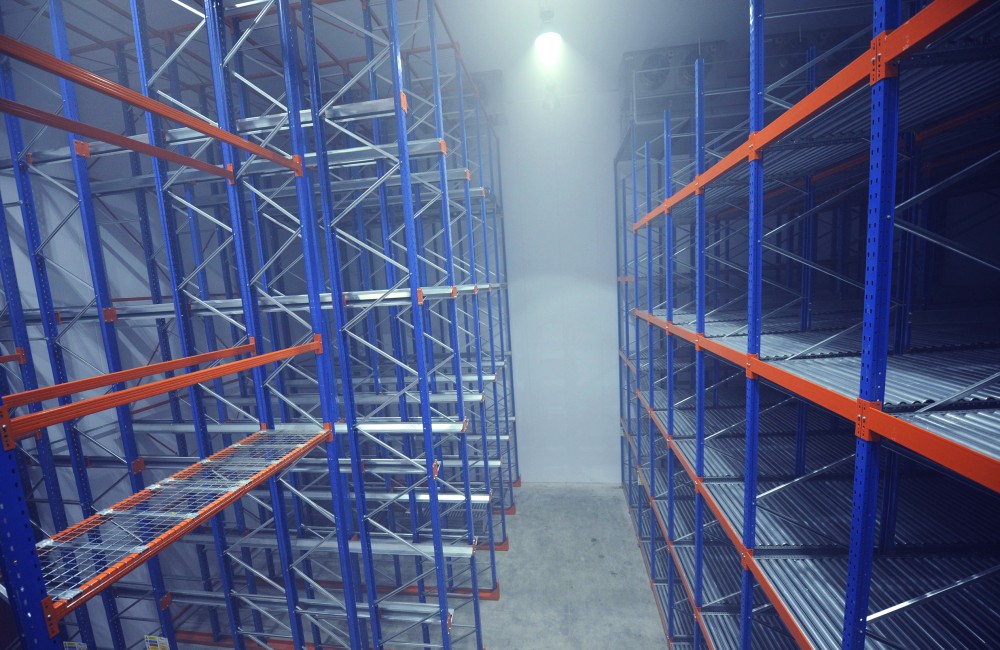
How It Works: Drive-in and drive-through racking systems involve forklifts entering the rack from one side (drive-in) or both sides (drive-through). Pallets are stored on rails, maximising storage capacity.
Pros and Cons:
- Pros: High storage density, suitable for bulk storage.
- Cons: Limited access to individual pallets, suitable for last-in, first-out (LIFO) inventory.
Ideal Applications: Perfect for businesses with large quantities of the same SKU and a high turnover rate.
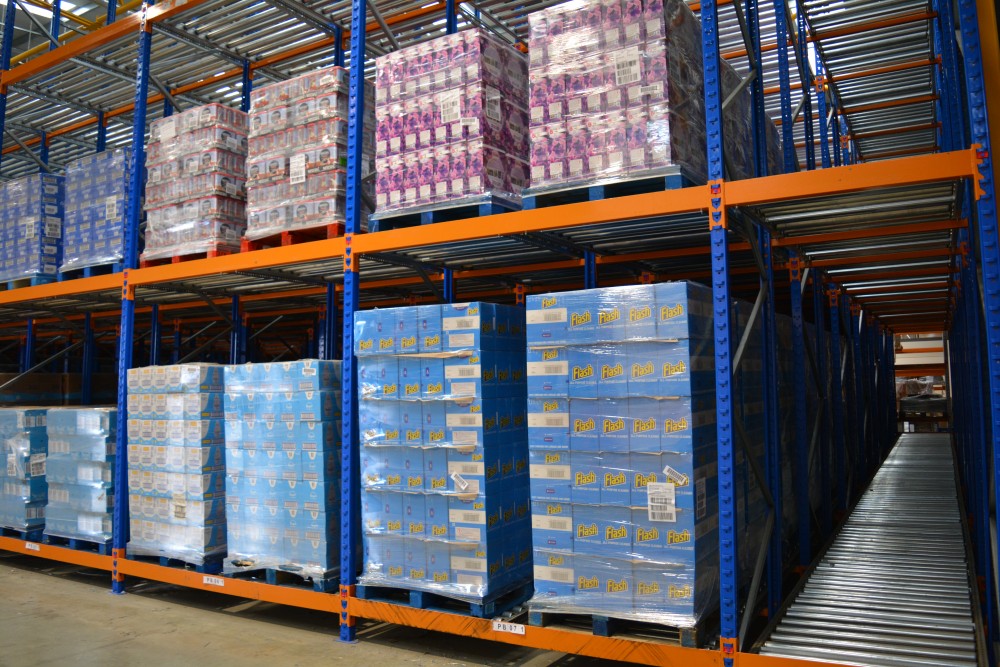
Overview: Push back racking utilises a system of nested carts on inclined rails. Pallets are loaded from the front, and as new pallets are added, the previous ones are pushed back.
Advantages:
- Maximises storage space by utilising depth.
- Maintains the selectivity of a standard pallet racking system.
Considerations: Requires a last-in, first-out (LIFO) inventory management approach.
Suitable Industries: Commonly used in food and beverage, manufacturing, and distribution.
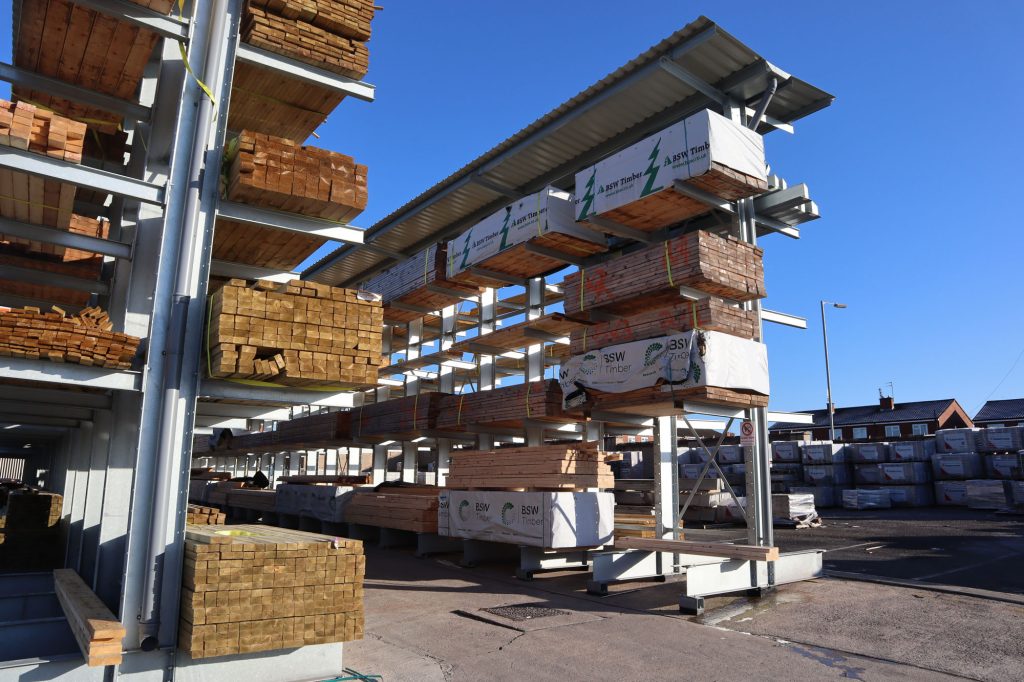
Understanding Cantilever Racking: Cantilever racking is designed for the storage of long and bulky items, such as timber, pipes, or furniture. It features horizontal arms extending from vertical columns.
Use Cases and Benefits:
- Ideal for items of varying lengths.
- Easy access for forklifts or crane systems.
Special Considerations: Suited for businesses dealing with non-standard or oversized items.
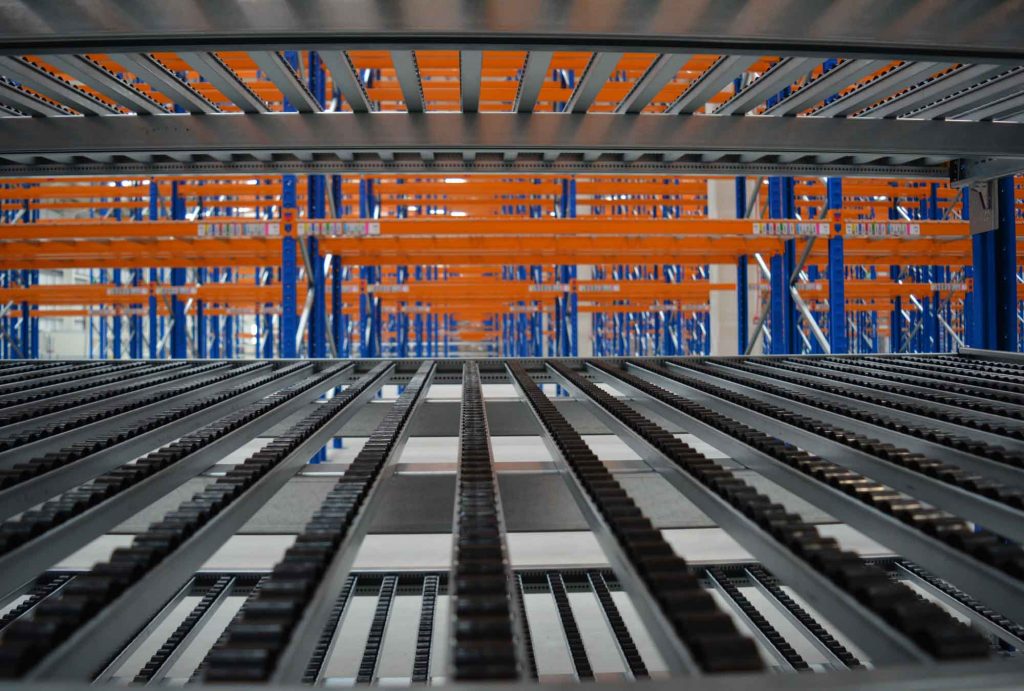
Understanding Carton Live Storage: Carton Live Storage Systems or Pallet Live Storage is a gravity-fed storage system where the cartons or pallets are stored on inclined racks, thus allowing a first-in/first-out, or a first-in/last-out Push Back operation to be followed.
What are the Benefits:
- Reduced walking
- First-in / First-out stock rotation is guaranteed
- Carton Live saves space by eliminating walkways
- Order Picking speeds and productivity improve vastly with Carton Live
- Stores high volumes of stock
- Can be automated
- Usually it works according to FIFO principle (First-In, First-Out)
- Inventory is easier to monitor and control
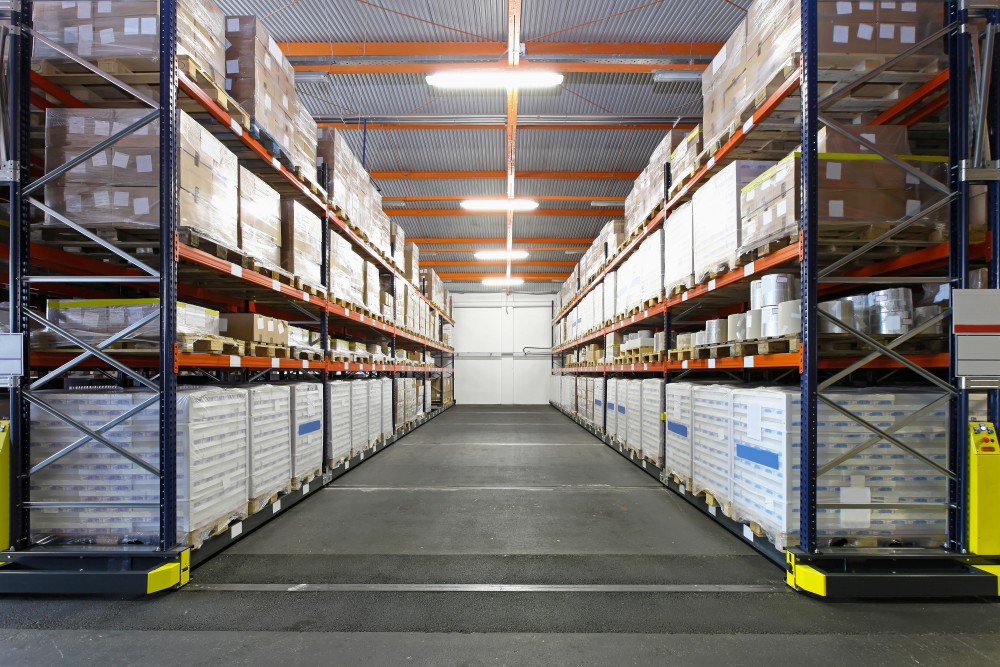
Understanding Mobile Solutions: Mobile Pallet Racking is the finest solution for High Density Storage, particularly for ambient warehouses and cold stores. Suitable for low temperatures down to -30º C.
Advantages of Mobile Racking Systems:
- Highly efficient use of space
- Computer-controlled storage
- Major increase in warehouse capacity
- Eliminate fixed access aisles
- Have access to all pallets without having to move any other pallets first
- No specialised trucks required
Our storage solutions are versatile and can also be used for offices, libraries, and hospitals as it is the ideal solution for archiving, filing storage, storing medical files.
Chapter 3: Pallet Racking Configurations
Choosing the right pallet racking configuration is a critical decision that directly impacts the efficiency of your warehouse operations. In this chapter, we will explore different pallet racking configurations, each designed to address specific storage needs and spatial constraints.
1. Single Deep Racking
Explanation: Single deep racking is the most common configuration, where pallets are stored one deep on each side of the aisle. This allows for direct access to every pallet position.
Benefits:
- Excellent selectivity and accessibility.
- Ideal for businesses with diverse products and a need for quick picking.
Suitable Applications: Perfect for retail, e-commerce, or any environment where quick access to individual pallets is essential.
2. Double Deep Racking
Overview of Double Deep Configurations: In double deep racking, pallets are stored two deep, requiring a forklift with extended reach to access the rear pallet. This configuration offers increased storage density compared to single deep racking.
Advantages and Considerations:
- Advantages: Higher storage density.
- Considerations: Reduced selectivity; best suited for slower-moving items.
Best Fit Scenarios: Ideal for businesses with larger quantities of the same SKU and a balance between selectivity and storage capacity.
3. Narrow Aisle Racking
Understanding Narrow Aisle Configurations: Narrow aisle racking optimises warehouse space by reducing aisle width and utilising tall, narrow aisles. Specialised forklifts, such as turret trucks or man-up trucks, navigate these aisles to access pallets.
Space-Saving Benefits:
- Maximises vertical storage space.
- Allows for high-density storage without sacrificing accessibility.
Industries that Benefit: Well-suited for facilities with limited floor space, high ceilings, and a need for efficient space utilisation.
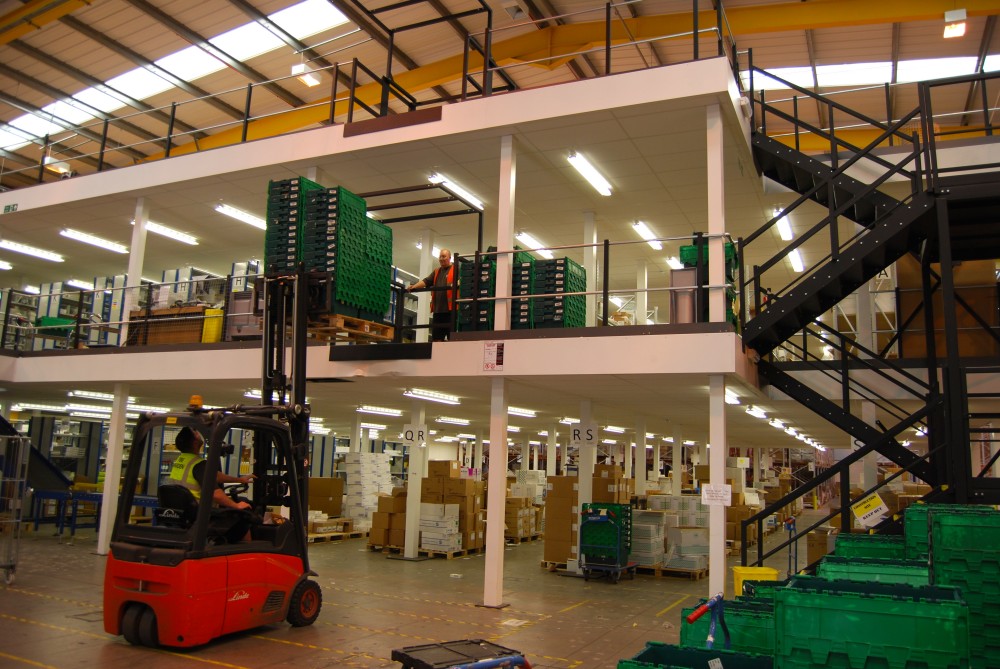
4. Multi-Tier Industrial Racking Systems
Explanation of Multi-Tier Systems: Multi-tier racking involves the construction of multiple levels of racking within a warehouse. It utilises mezzanine structures to create additional storage space above ground level.
Advantages and Limitations:
- Advantages: Maximizes vertical space, creates additional picking levels.
- Limitations: Higher upfront costs; suitable for large-scale operations.
Ideal Situations: Ideal for e-commerce fulfillment centers and facilities with a high volume of order picking.
Selecting the appropriate pallet racking configuration depends on factors such as the nature of your products, warehouse space, and operational requirements. In the next chapter, we will delve into essential tips for the installation of pallet racking systems to ensure safety and optimal functionality.
Chapter 4: Installation Tips
Installing pallet racking systems requires careful planning, precision, and adherence to safety standards. In this chapter, we will guide you through the essential tips for a successful pallet racking installation, covering everything from site preparation to regulatory compliance.
1. Site Preparation
Preparing the Space:
- Clear the Area: Ensure the installation site is clear of obstacles, debris, and other materials that may impede the installation process.
- Floor Inspection: Conduct a thorough inspection of the floor to ensure it can support the weight of the pallet racking system and its intended load.
- Emergency Exits: Maintain clear paths to emergency exits, fire extinguishers, and other safety equipment.
- Lighting: Ensure proper lighting in the installation area to enhance visibility and safety during the process.
2. Assembly and Installation
Step-by-Step Guide:
- Follow Manufacturer Guidelines: Adhere to the manufacturer’s guidelines and instructions for assembly and installation.
- Secure Anchoring: Ensure the pallet racking system is securely anchored to the floor to prevent instability.
Safety Measures:
- Personal Protective Equipment (PPE): Require installation personnel to wear appropriate PPE, including helmets, gloves, and safety vests.
- Training: Provide comprehensive training for the installation team on safety procedures and protocols.
3. Regulatory Compliance
Local Regulations and Standards:
- Permitting: Check and obtain any necessary permits required for the installation of pallet racking systems in your location.
- Compliance Checks: Ensure compliance with local building codes, fire safety regulations, and seismic requirements.
Safety and Legality:
- Load Capacity: Verify that the installed pallet racking system adheres to load capacity specifications outlined by the manufacturer.
- Inspections: Schedule regular inspections to ensure ongoing compliance with safety standards.
Installing pallet racking systems is a critical phase in creating an efficient and safe warehouse environment.
By carefully preparing the site, following precise assembly procedures, and staying compliant with regulations, you set the foundation for a robust storage solution.
In the next chapter, we will explore best practices for maintaining pallet racking systems to ensure their longevity and optimal performance.
Chapter 5: Maintenance Best Practices
Maintaining pallet racking systems is essential for ensuring their longevity, safety, and continued efficiency. This chapter will outline key maintenance best practices.
Frequency:
- Conduct routine inspections at regular intervals.
- Schedule annual or semi-annual comprehensive inspections.
Checklist:
- Inspect upright frames for signs of damage, such as bending or twisting.
- Examine beams for warping or deflection.
- Ensure that safety clips are intact and functioning properly.
- Check for any visible signs of corrosion or rust.
2. Repairs and Upgrades
Prompt Addressing of Issues:
- Immediately address any identified issues during inspections.
- Replace damaged components promptly to maintain structural integrity.
Upgrading for Efficiency:
- Consider system upgrades to accommodate changing storage needs.
- Upgrade safety features, such as adding additional column guards or pallet stops.
3. Training for Staff
Importance of Training:
- Provide comprehensive training for warehouse personnel on proper use and care of the pallet racking system.
- Train staff on identifying potential issues during routine tasks.
Ongoing Training Programs:
- Implement ongoing training programs to keep staff updated on safety protocols and system changes.
- Foster a culture of safety awareness among warehouse personnel.
Implementing these installation and maintenance best practices is essential for the long-term success of your pallet racking systems. In the next chapter, we will explore real-world case studies to highlight successful pallet racking implementations and the lessons learned from them.
Chapter 6: Case Studies of Racking Systems
Conclusion
Congratulations on completing the Ultimate Guide to Pallet Racking Systems! We hope this comprehensive resource has been instrumental in enhancing your understanding of pallet racking systems, from the various types and configurations to installation tips and maintenance best practices.
By now, you should have a clear grasp of the factors influencing the choice of pallet racking systems, allowing you to make informed decisions that align with your business requirements. Whether you’re a warehouse manager aiming to improve operational efficiency or a business owner seeking space optimisation, implementing the insights from this guide will undoubtedly contribute to the success of your storage strategy.
As you embark on your journey to leverage pallet racking systems for maximum efficiency, remember the importance of ongoing learning and adaptation. The world of logistics is ever-evolving, and staying informed about the latest trends and technologies will empower you to stay ahead of the curve.
Thank you for entrusting us with your exploration of pallet racking systems. We wish you success in implementing these strategies and creating a warehouse environment that fosters efficiency, safety, and growth.
Here’s to a future of optimised storage and streamlined logistics!